As the summer’s sweltering 40°C plus temperatures continue to sweep across Europe and other parts of the world, we all look forward to enjoying a refreshing ice cream (or two!) as we try to stay cool. Which, of course means freezers are having to work overtime…
In freezers, heat is removed from the air, causing any moisture to condense and form frost on the cold evaporator coils. As the frost accumulates, industrial refrigeration systems can find their energy consumption is significantly affected. Acting as an insulating layer, the frost reduces heat transfer efficiency, increasing compressor workload, which in turn consumes more energy, generating higher costs. To mitigate this, efficient defrost is essential.
How it works
There are two common methods: electrical/resistant defrost and defrost with brine. The electrical defrost involves the use of electric heaters installed on the evaporator coils. This results in frost evaporation rather than melting, which increases the air humidity and easily allows the frost to build up again. While this method is straightforward with low initial costs, it consumes electrical energy, leading to increased operating costs.
In the brine defrost system, the brine is heated using a separate heat source, such as hot refrigerant gas, hot water, or any other waste heat. This heats the brine and increases its temperature. This heated brine is then circulated through pipes which are in contact with the evaporator coils, melting the frost and draining the water to the sewer.
An excellent defrost brine is CRANE Temper, which has superior thermal properties, is energy efficient and non-toxic.
Pros and cons
Defrost with brine is often preferred in industrial settings due to its energy efficiency. It consumes less energy compared to electrical defrost, resulting in significant cost savings.
Brine defrost systems also offer reduced downtime as they require shorter defrost cycles, enabling the freezer to resume normal operations quickly. Environmentally, defrost with brine reduces reliance on electricity and decreases greenhouse gas emissions. In addition, brine solutions can be formulated with environmentally friendly and non-toxic antifreeze agents, like CRANE Temper, promoting sustainability.
However, implementing a brine defrost system requires a more complex and costly initial setup, involving separate circulation systems, additional infrastructure, pipes and pumps.
In conclusion
Considering both methods, while defrost with brine offers energy efficiency, reduced downtime, environmental benefits and flexibility, there is an initial installation complexity and cost. At the same time, operating costs are low. With electrical/resistant defrost, over time the overall costs will be higher.
Case study
An energy study for the defrost of a CO2 evaporator installation was done by Descals in Spain. The installation consists of two freezers, operating at -25°C and -44°C respectively, using CO2 as a refrigerant.
When comparing the initial investment cost for an electrical and CRANE Temper installation, CRANE Temper had a higher initial cost of approximately EUR 86.800 (net).
When comparing the energy consumption, the CRANE Temper installation required energy for the pumps to the defrost loop only, corresponding to an annual energy cost (based on the market conditions when the study was made) of approx. EUR 1.200.
The same annual energy cost for an electrical defrost installation was EUR 28.800.
With a higher installation cost for the CRANE Temper installation, but with a substantially lower annual energy cost, the overall cost of the installation would be recovered in 3 years.
After running the installation for 10 years, the lower energy consumption has not only saved natural resources, but almost EUR 300.000. The study is illustrated below:
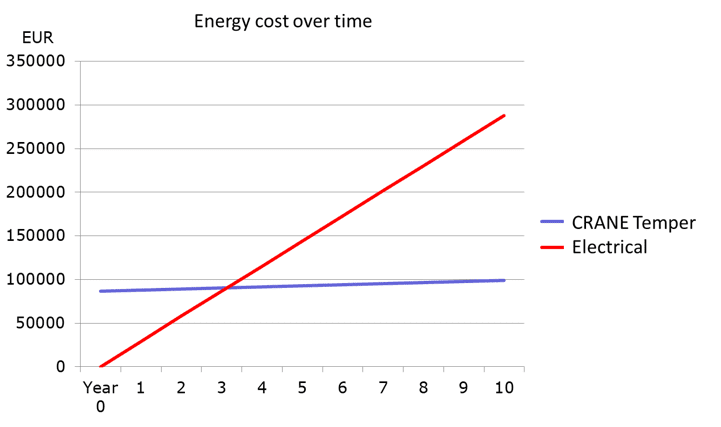
The significant cost savings add up to a lot of ice creams… something to consider the next time you’re enjoying your ice cream in the sun.
Latest News
Trade Affiliations
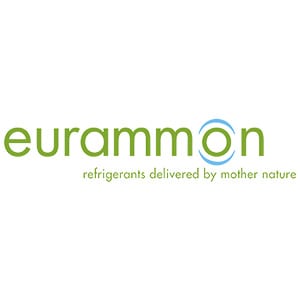
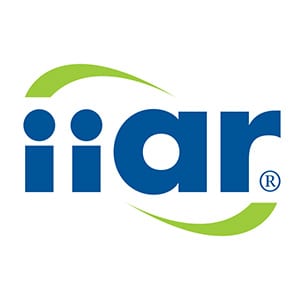
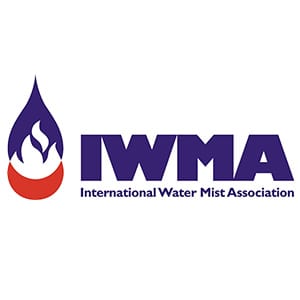
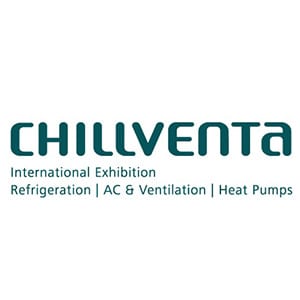
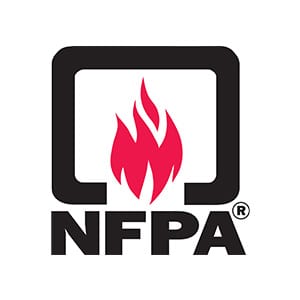

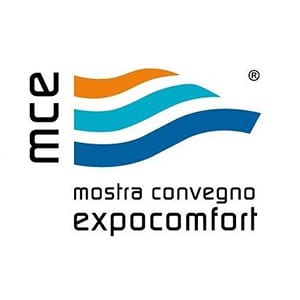

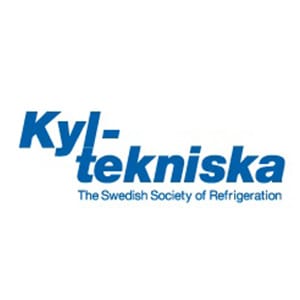
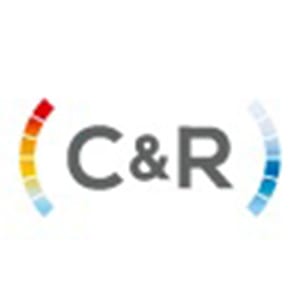